Many industrial applications use industrial pumps for manufacturing processes and water treatment facilities. However, the machinery nature of industrial pumps can often encounter efficiency-reducing and performance-affecting technical problems.
Identifying standard problems in industrial pumps enables organizations to minimize equipment downtime and prolong their operational life. The following section details standard problems industrial pumps face, along with feasible solutions from our Pumpbiz pump experts.
Pump not starting
A failed start indicates possible problems with electrical components, motor failure, or a stuck impeller.
How to fix it:
- Check the power supply and reactivate any electricity circuits that have tripped.
- Examine the motor components for any issues and decide whether to replace it.
- Check the impeller for any debris and examine its ability to rotate without restrictions.
Leakage
Unguarded leaks inside industrial pumps result in fluid loss, which produces operational inefficiencies and creates possible safety risks. The main culprits behind these problems are damaged seals, snapped pump housings, and loose connections.
How to fix it:
- Perform regular inspections of seals and replace them before their condition deteriorates.
- Examine the pump housing for cracks then repair or replace all bad components.
- Examine all loose fastenings and verify that gaskets are installed correctly.
Cavitation
Pump operation at low pressures forms air bubbles known as cavities that damage impellers and lower system efficiency. Pumps showing signs of cavitation have excessive noise, increased vibration, and decreased flow rate.
How to fix it:
- Regularly check fluid levels and position the pump properly to minimize problems with suction pressure.
- Slow down the pump speed when excessive speed operations occur.
- A bigger diameter suction pipe will help prevent pressure drops.
Overheating
High temperatures can degrade pump components. This results in equipment failures that cost the system more in maintenance expenses. Inadequate lubrication, system overloads, and obstructed cooling mechanisms can result in overheating.
How to fix it:
- Follow manufacturer guidelines to properly lubricate the pump system.
- The pump should function at rates that fit within its recommended capacity range.
- Clean heat exchangers, cooling fans, and filters regularly to prevent overheating.
Reduced flow or pressure
A low flow rate accompanied by reduced pressure indicates possible areas of blockage, damaged impellers, or size incompatibility between the pump design and application requirements. Such issues result in operation inefficiencies, which negatively affect productivity.
How to fix it:
- Look for debris blockages in both suction and discharge pipelines and remove them.
- Assess the impeller state to determine if replacement is needed.
- Ensure that the pump matches the specifications needed for its application.
More noise and vibration
Vibration and abnormal pump sounds often signal that the equipment has misaligned parts, loose components, or worn-out bearings. Procrastinating with these warning signals results in extreme consequences.
How to fix it:
- Use precision tools to properly align the motor and pump unit.
- Check and tighten all loose hardware and components.
- Examine and substitute bearings that show wear to stop additional damage.
A key takeaway
Regular maintenance and fast troubleshooting help prevent major issues that might arise from industrial pump failures.
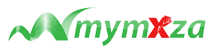